Understanding China Injection Molding: A Comprehensive Guide
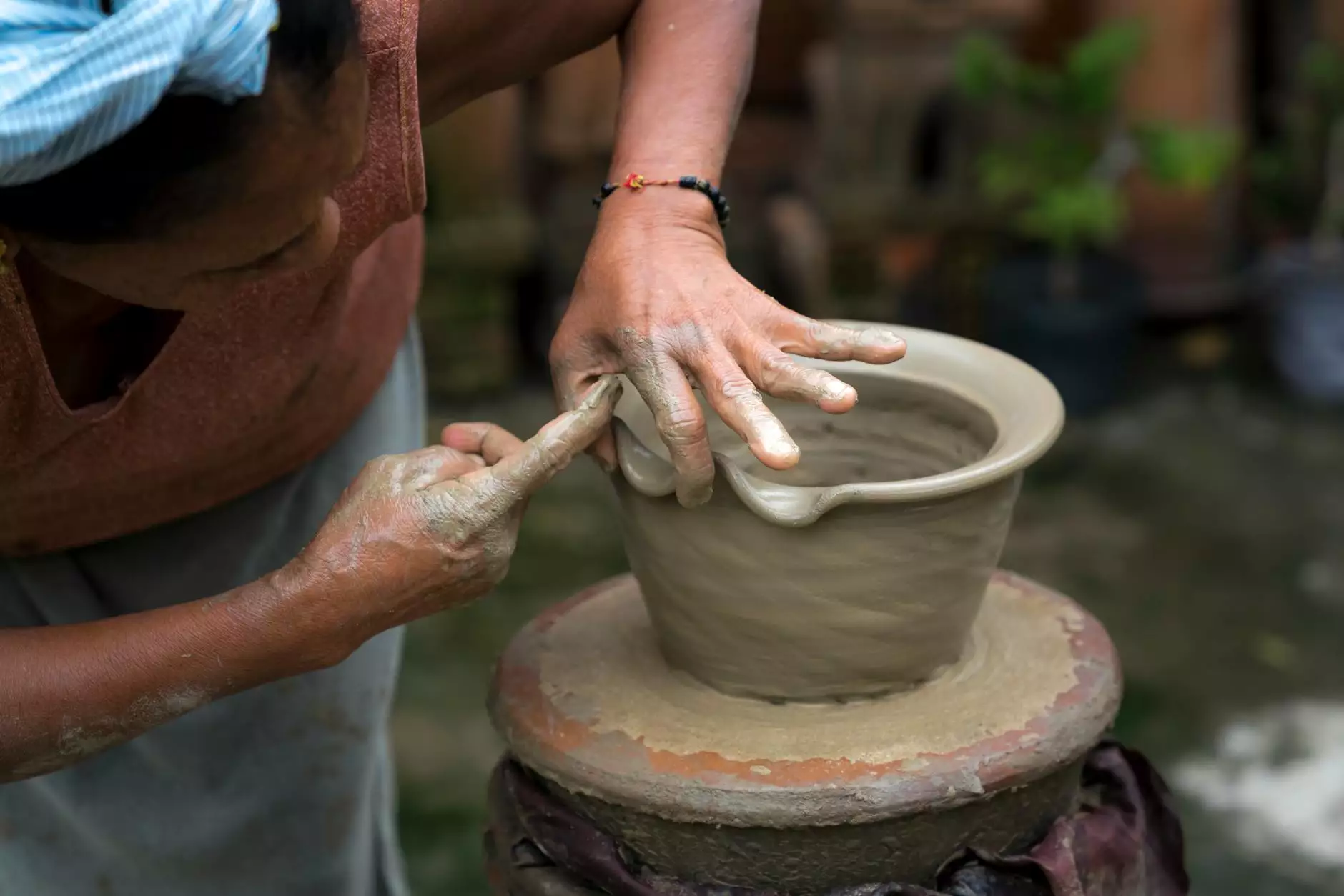
China injection molding has become a cornerstone of modern manufacturing, expanding its influence in various industries around the globe. As a vital component in the production process, this method offers a multitude of benefits that can drive innovation and efficiency for businesses. In this article, we will dive deep into the world of injection molding in China, explore its advantages, processes, applications, and why Deep Mould might be your ideal partner in this journey.
The Basics of Injection Molding
Injection molding is a manufacturing process used for producing parts by injecting molten material into a mold. The materials commonly used in injection molding include plastics, metals, glass, and ceramics. The technique is characterized by its ability to create complex shapes and designs with high precision and minimal waste.
Why Choose China for Injection Molding?
1. Cost-Effectiveness
One of the primary reasons businesses opt for China injection molding is cost-effectiveness. China has a well-established manufacturing ecosystem that allows companies to produce high volumes at considerably lower costs than many Western countries. This cost advantage is primarily due to:
- Lower Labor Costs: The cost of labor in China is significantly lower, which reduces overall production costs.
- Economies of Scale: China’s vast manufacturing capacity enables companies to benefit from economies of scale, passing on savings to customers.
- Access to Advanced Technology: Chinese manufacturers are increasingly adopting advanced technologies, ensuring high-quality production at lower costs.
2. Expertise and Experience
China boasts a long history in manufacturing and has developed a pool of experienced professionals in the field of injection molding. The expertise of manufacturers in China ensures that the quality meets international standards, and they are constantly innovating to improve processes and products.
3. Versatility of Materials
Injection molding in China allows for a wide variety of materials to be used, including:
- Thermoplastics: These can be melted and re-shaped multiple times, making them ideal for recycling.
- Thermosetting Plastics: These materials can only be shaped once, providing excellent durability and heat resistance for specific applications.
- Metals: Injection molding techniques have advanced to include metal materials, offering new possibilities in product design.
The Injection Molding Process
The China injection molding process can be broken down into several crucial steps, each playing a vital role in ensuring the quality and efficiency of the final product:
1. Designing the Mold
The first step in the injection molding process is designing the mold. This involves:
- Creating a 3D CAD model of the part to be produced.
- Considering the specific characteristics required for the final product, such as strength and flexibility.
2. Mold Fabrication
Once the design is approved, the next step is fabricating the mold. This is typically done using:
- CNC Machining: Using computer-controlled machines to manufacture the mold with high precision.
- EDM (Electrical Discharge Machining): This is used for creating intricate shapes and details within the mold.
3. Material Preparation
The selected material is prepared, typically in the form of pellets, which are then heated until they melt. This molten material is crucial for the upcoming step.
4. Injection Process
The liquid material is injected into the mold under high pressure. This ensures that the material fills all cavities, producing a detailed part. The pressure also reduces the chance of air bubbles, ensuring the strength of the final product.
5. Cooling Time & Ejection
Once the mold is filled, it is cooled to allow the material to solidify. After a specific cooling period, the mold opens, and the finished part is ejected.
Applications of Injection Molding
The versatility of China injection molding means it finds applications across numerous industries:
1. Automotive Industry
Injection molding is widely used in the production of various components such as dashboards, bumpers, and panels, which require high precision and durability.
2. Consumer Electronics
From mobile phone casings to computer components, injection molding produces small, intricate parts that meet high standards of functionality and aesthetics.
3. Medical Devices
The medical industry relies on injection molding for producing sterile and precise components such as syringes, surgical instruments, and various disposables.
4. Packaging Industry
Injection molding is also employed in creating packaging materials and containers that are both functional and appealing to consumers.
Quality Control in China Injection Molding
Quality control is a critical aspect of the injection molding process in China. Here’s how it is implemented:
1. Inspections at Every Stage
Manufacturers conduct inspections throughout the entire process—from mold design to the final production stage—to ensure conformity to specifications.
2. Use of Advanced Testing Equipment
Advanced equipment is vital for testing strength, durability, and other parameters to ensure the parts meet international quality standards.
3. Continuous Improvement Programs
Many Chinese manufacturers adopt lean manufacturing principles to continuously improve their processes, reducing waste and enhancing quality.
Partnering with Deep Mould for Superior Injection Molding Solutions
Deep Mould is a leader in the field of injection molding in China. Here’s why you should consider partnering with us:
- Expertise: Our team comprises seasoned professionals with extensive experience in injection molding.
- State-of-the-Art Facility: Equipped with the latest technology to ensure high-quality production.
- Commitment to Quality: We adhere to stringent quality control measures to guarantee the best products for our clients.
- Custom Solutions: We offer tailored solutions to meet the specific needs of your business.
Conclusion
In summary, China injection molding presents immense opportunities for businesses looking to enhance their manufacturing capabilities. With its cost-effectiveness, versatility, and efficiency, it is the ideal solution for producing high-quality plastic and metal parts. By choosing to collaborate with established players like Deep Mould, you can ensure superior outcomes in your projects and drive your business forward in an increasingly competitive landscape.
Explore our services at Deep Mould and discover how we can assist you in achieving your manufacturing goals.